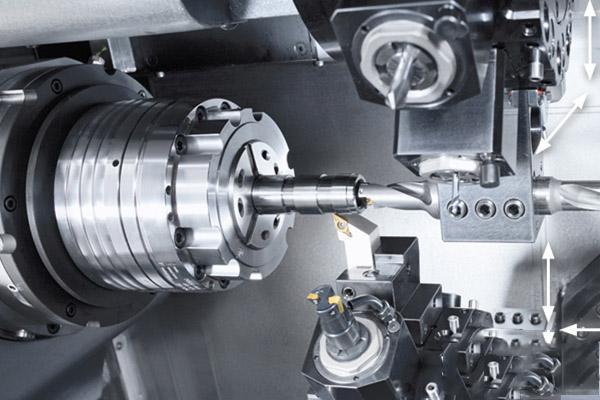
Thread Milling Improves Asymmetric Machining Efficiency
Thread is a common connection structure in mechanical parts, and its processing quality and efficiency directly affect the performance and cost of parts.
The traditional thread processing methods mainly include tap tapping, thread turning and thread picking, etc.
These methods are relatively mature and convenient for processing cylindrical threads with symmetrical profiles, but when processing cylindrical threads with asymmetrical profiles, they will encounter problems to many difficulties and problems, such as:
1. When the tap is tapping, due to the unbalanced cutting force of the asymmetric tooth profile, the tap is easily twisted or broken, resulting in poor thread quality or scrapped workpiece.
2. During thread turning, due to the different cutting depths of asymmetric tooth profiles, it is necessary to enter the tool multiple times or adjust the tool angle, which increases the processing time and difficulty.
3. When thread picking, due to the high precision requirements for the tool manufacturing of the asymmetric tooth profile, and the need for multiple tools to be used together, the tool cost and tool change time are increased.
“Save 50% on the same quality”
In order to solve these problems, this paper proposes a method to improve the machining efficiency of asymmetric parts by thread milling.
Thread milling is to use a thread milling cutter to process threads in a three-axis linkage milling method on a CNC machining center. It has the following advantages:
1. Fast processing speed, high efficiency and high processing precision. The tool material is generally cemented carbide material, and the cutting speed is fast. The tools are manufactured with high precision, so the milled threads are milled with high precision.
2. Milling tools have a wide range of applications. As long as the pitch is the same, no matter it is a left-handed thread or a right-handed thread, one tool can be used, which is beneficial to reduce the cost of the tool.
3. Milling is easy to remove chips and cool. Compared with taps, the cutting condition is better. It is especially suitable for thread processing of difficult-to-machine materials such as aluminum, copper, and stainless steel.
4. Because there is no guidance from the front end of the tool, it is suitable for machining blind holes with short thread bottom holes and holes without tool relief.
In order to verify the effectiveness of the method proposed in this paper, this paper takes the asymmetric profile cylindrical thread M48×1.5 as an example to carry out numerical control simulation and experimental verification.
The results show that the thread milling method can greatly improve the processing efficiency and reduce the cost while ensuring the thread quality.
To sum up, thread milling technology has obvious advantages in the thread processing of asymmetric parts.
It can not only improve processing quality and precision, but also save processing time and cost, and improve production efficiency and competitiveness.
In order to give full play to the potential of thread milling technology, it is necessary to pay attention to the selection of appropriate tools, cutting parameters, processing routes, programming skills and other factors, while also considering machine tool performance, workpiece materials, cooling and lubrication and other conditions.
Only by comprehensively using thread milling technology can efficient thread processing of asymmetric parts be realized.
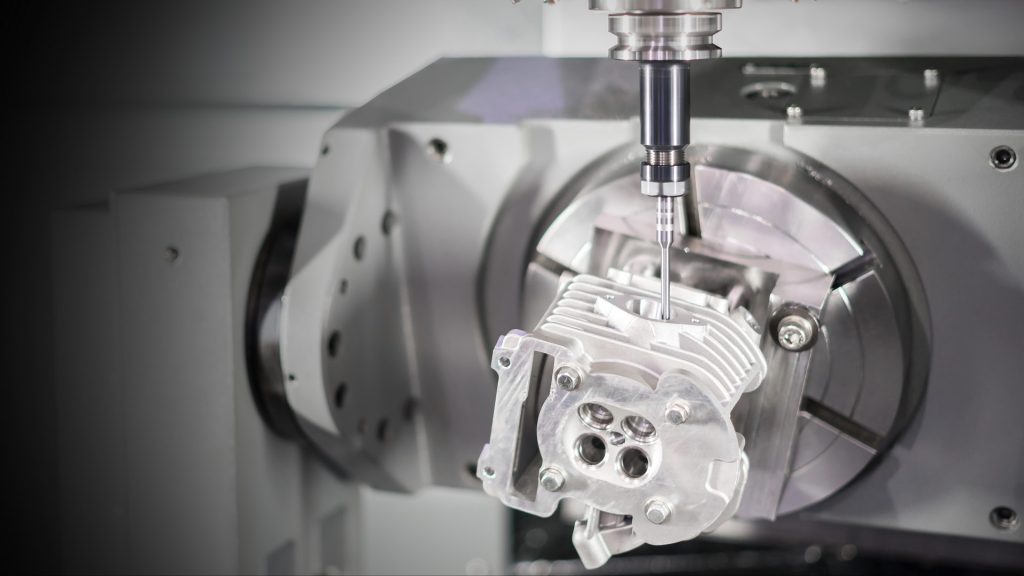
Leave a Reply