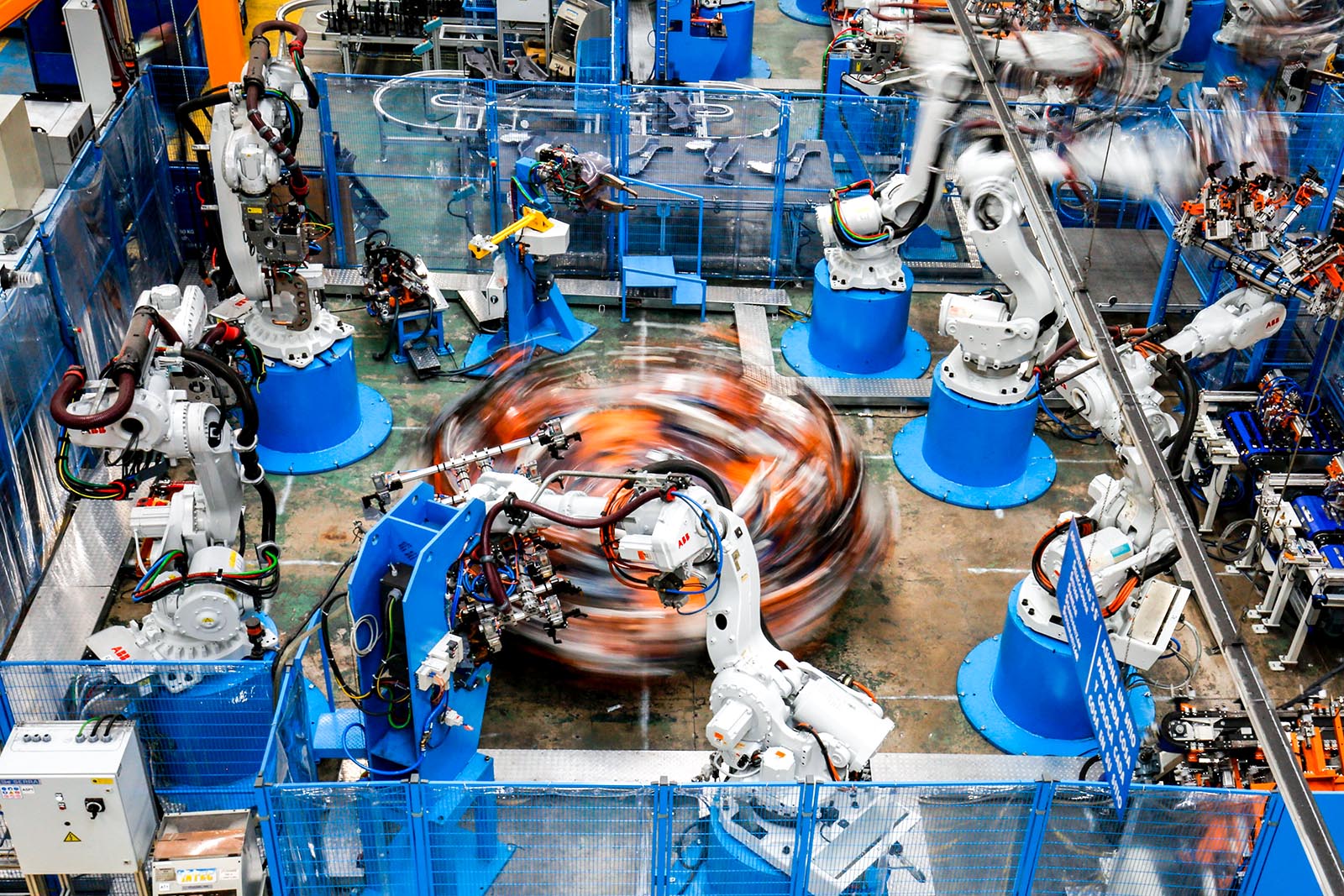
Technical Standards and Quality Management of Precision Tool Manufacturing
Precision tools refer to tools capable of processing, measuring, testing, etc. at the micron or nanometer level, and they are widely used in various industries. Precision tool manufacturing refers to the process of using various advanced technologies and equipment to produce precision tools that meet customer needs and market competition in accordance with certain technical standards and quality management systems. Precision tool manufacturing is a high-tech, high-value-added, high-quality manufacturing activity, which is of great significance to improving the level of my country’s manufacturing industry and international competitiveness. This article will introduce the technical standards and quality management of precision tool manufacturing from the following aspects.
“Technical standards for precision tool manufacturing”
Technical standards refer to normative documents that specify the technical requirements, performance indicators, test methods, etc. of products or services. It is the basis for ensuring the quality and safety of products or services. The technical standards for precision tool manufacturing mainly include the following categories:
National standard: Refers to technical standards formulated and published by the National Standardization Management Committee or its authorized organizations, applicable nationwide, such as GB/T 1804-2000 “General Tolerance Limits and Coordination”.
Industry standard: refers to the technical standard formulated and issued by the relevant state department or its authorized organization, which is applicable to a specific industry or field, such as JB/T 5000.8-2007 “General Technical Conditions for Heavy Machinery Part 8: Precision Inspection”.
Enterprise standard: refers to the technical standards formulated and released by the enterprise itself, which are applicable to the internal or external transactions of the enterprise, such as Q/320282JZ001-2016 “Technical Conditions for Precision Cutting Tools”.
International standard: Refers to the technical standards formulated and published by the International Organization for Standardization or its member organizations, applicable worldwide, such as ISO 230-1:2012 “Testing Machine Tools Part 1: Geometric Accuracy Inspection”.
The manufacture of precision tools should follow relevant technical standards to ensure the quality and safety of products or services, and it is also conducive to improving production efficiency and reducing costs. Precision tool manufacturing enterprises should choose appropriate technical standards according to their own production characteristics and market demand, and constantly track and master the updates and changes of technical standards to adapt to market competition and customer needs.
National standard: Refers to technical standards formulated and published by the National Standardization Management Committee or its authorized organizations, applicable nationwide, such as GB/T 1804-2000 “General Tolerance Limits and Coordination”.
Industry standard: refers to the technical standard formulated and issued by the relevant state department or its authorized organization, which is applicable to a specific industry or field, such as JB/T 5000.8-2007 “General Technical Conditions for Heavy Machinery Part 8: Precision Inspection”.
Enterprise standard: refers to the technical standards formulated and released by the enterprise itself, which are applicable to the internal or external transactions of the enterprise, such as Q/320282JZ001-2016 “Technical Conditions for Precision Cutting Tools”.
International standard: Refers to the technical standards formulated and published by the International Organization for Standardization or its member organizations, applicable worldwide, such as ISO 230-1:2012 “Testing Machine Tools Part 1: Geometric Accuracy Inspection”.
Technical standards refer to normative documents that specify the technical requirements, performance indicators, test methods, etc. of products or services. It is the basis for ensuring the quality and safety of products or services. The technical standards for precision tool manufacturing mainly include the following categories:
National standard: Refers to technical standards formulated and published by the National Standardization Management Committee or its authorized organizations, applicable nationwide, such as GB/T 1804-2000 “General Tolerance Limits and Coordination”.
Industry standard: refers to the technical standard formulated and issued by the relevant state department or its authorized organization, which is applicable to a specific industry or field, such as JB/T 5000.8-2007 “General Technical Conditions for Heavy Machinery Part 8: Precision Inspection”.
Enterprise standard: refers to the technical standards formulated and released by the enterprise itself, which are applicable to the internal or external transactions of the enterprise, such as Q/320282JZ001-2016 “Technical Conditions for Precision Cutting Tools”.
International standard: Refers to the technical standards formulated and published by the International Organization for Standardization or its member organizations, applicable worldwide, such as ISO 230-1:2012 “Testing Machine Tools Part 1: Geometric Accuracy Inspection”.
The manufacture of precision tools should follow relevant technical standards to ensure the quality and safety of products or services, and it is also conducive to improving production efficiency and reducing costs. Precision tool manufacturing enterprises should choose appropriate technical standards according to their own production characteristics and market demand, and constantly track and master the updates and changes of technical standards to adapt to market competition and customer needs.
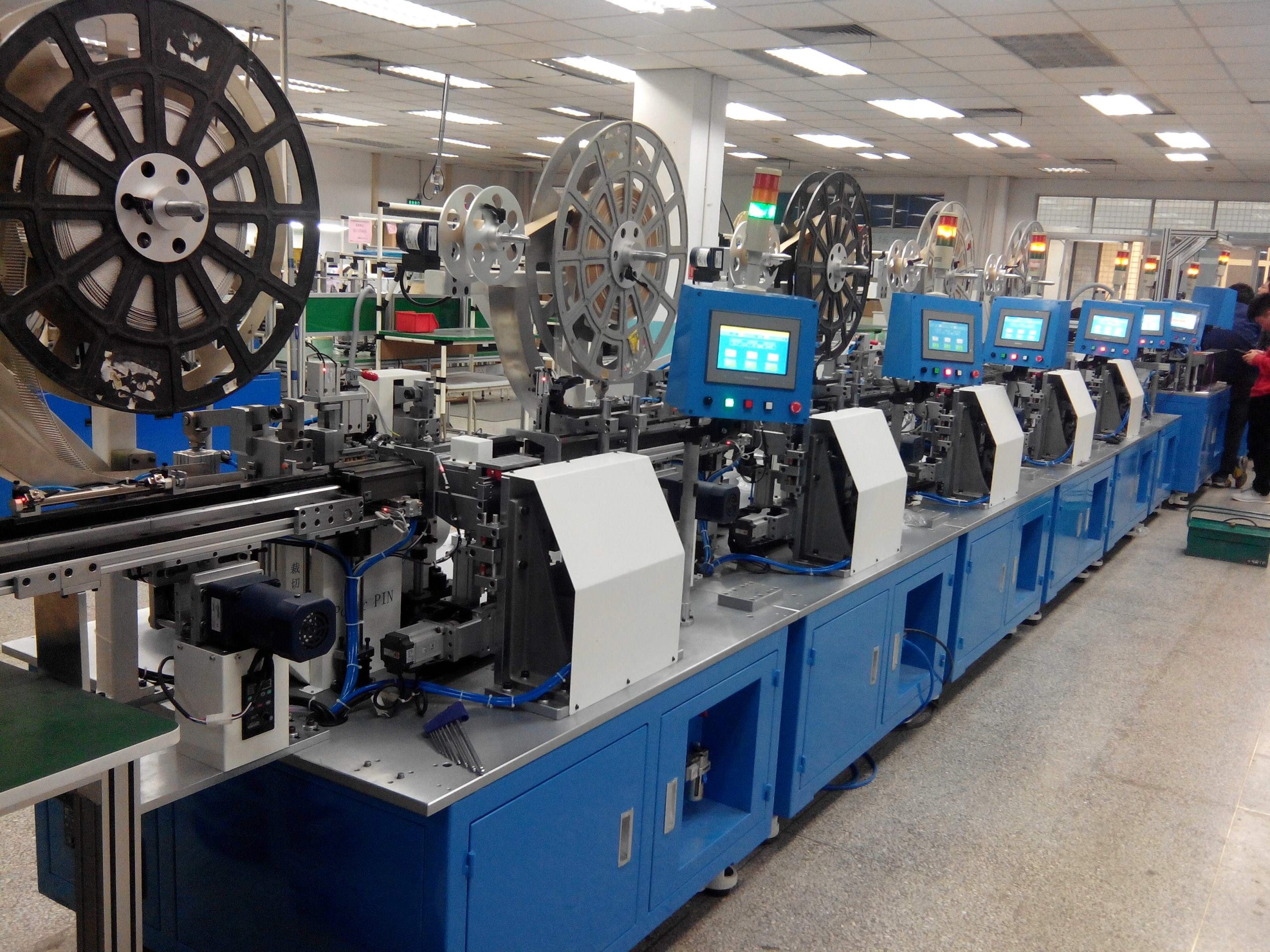
Quality management of precision tool manufacturing
Quality management refers to the process of controlling and guaranteeing the quality of products or services through planning, organizing, implementing, inspecting, improving and other activities. The quality management of precision tool manufacturing mainly includes the following aspects:
Quality planning: before the development and production of products or services, according to customer needs and market competition, determine the quality objectives, quality requirements, quality control methods and other content of products or services, so as to ensure that the quality of products or services meets expectations. The quality planning of precision tool manufacturing should include the following steps:
Determine the quality objectives of the product or service, such as accuracy, reliability, lifespan, etc.
Determine the quality requirements of products or services, such as technical standards, regulatory specifications, customer requirements, etc.
Determine the quality control methods of products or services, such as inspection and testing methods, quality recording methods, quality analysis methods, etc.
Determine the quality control resources of products or services, such as personnel, equipment, materials, environment, etc.
Prepare quality control plans for products or services, such as process flow charts, control plans, work instructions, etc.
Quality control: refers to the activities of monitoring and adjusting the quality of products or services in accordance with the quality control plan during the development and production of products or services, so as to ensure that the quality of products or services meets expectations. The quality control of precision tool manufacturing should include the following steps:
Execute the quality control plan of products or services, and inspect and test the quality of products or services in accordance with prescribed methods and standards.
Record the quality data of products or services, such as inspection and testing results, processing results of non-conforming products, changes in process parameters, etc.
Analyze the quality data of products or services, such as using statistical process control (SPC) methods to conduct process capability analysis and stability analysis on the quality of products or services.
Take measures to improve the quality of products or services, such as using seven tools (histogram, cause and effect diagram, Pareto diagram, control chart, scatter diagram, flow chart, checklist) and other methods to check the quality of products or services identification and problem solving.
Quality assurance: Refers to the activities of standardizing and supervising the quality management activities of the entire organization by establishing and implementing a quality management system that meets international standards or industry standards, so as to ensure that the organization can continue to provide products that meet customer needs and market competition or service. The quality assurance of precision tool manufacturing should include the following steps:
Establish the organization’s quality policy and goals, such as following the principles of customer-oriented, continuous improvement, and full participation, to determine the quality level and direction pursued by the organization.
Establish the organization’s quality management system, such as preparing the organization’s quality manual, program documents, work instructions and other documents according to ISO 9001:2015 “Quality Management System Requirements” or IATF 16949:2016 “Automobile Industry Quality Management System Requirements” and other standards, And establish the corresponding organizational structure and distribution of responsibilities.
To implement the organization’s quality management system, such as carrying out various quality management activities in accordance with the provisions of the document, and conducting internal audits and management reviews to check and evaluate the effectiveness and applicability of the quality management system.
Improve the organization’s quality management system, such as using the PDCA (plan, execute, check, improve) cycle method to continuously improve the quality management system based on the results of internal audits and management reviews, as well as customer feedback and market changes.
Quality audit: Refers to the activities of inspecting and evaluating the quality management system of an organization or the quality of products or services through independent third-party agencies or personnel to verify whether the organization complies with relevant standards or requirements. The quality audit of precision tool manufacturing mainly includes the following categories:
System audit: refers to the audit of the organization’s quality management system, such as passing ISO 9001:2015 “Quality Management System Requirements” or IATF 16949:2016 “Automotive Industry Quality Management System Requirements” and other standards to certify the organization’s quality management system Audit to obtain the corresponding certification certificate.
Process audit: refers to the audit of a specific process or activity of the organization, such as the audit of the organization’s measurement process through ISO 10012:2003 “Measurement Management System Requirements”, to verify whether the measurement process meets the relevant requirements.
Quality management refers to the process of controlling and guaranteeing the quality of products or services through planning, organizing, implementing, inspecting, improving and other activities. The quality management of precision tool manufacturing mainly includes the following aspects:
Quality planning: before the development and production of products or services, according to customer needs and market competition, determine the quality objectives, quality requirements, quality control methods and other content of products or services, so as to ensure that the quality of products or services meets expectations. The quality planning of precision tool manufacturing should include the following steps:
Determine the quality objectives of the product or service, such as accuracy, reliability, lifespan, etc.
Determine the quality requirements of products or services, such as technical standards, regulatory specifications, customer requirements, etc.
Determine the quality control methods of products or services, such as inspection and testing methods, quality recording methods, quality analysis methods, etc.
Determine the quality control resources of products or services, such as personnel, equipment, materials, environment, etc.
Prepare quality control plans for products or services, such as process flow charts, control plans, work instructions, etc.
Quality control: refers to the activities of monitoring and adjusting the quality of products or services in accordance with the quality control plan during the development and production of products or services, so as to ensure that the quality of products or services meets expectations. The quality control of precision tool manufacturing should include the following steps:
Execute the quality control plan of products or services, and inspect and test the quality of products or services in accordance with prescribed methods and standards.
Record the quality data of products or services, such as inspection and testing results, processing results of non-conforming products, changes in process parameters, etc.
Analyze the quality data of products or services, such as using statistical process control (SPC) methods to conduct process capability analysis and stability analysis on the quality of products or services.
Take measures to improve the quality of products or services, such as using seven tools (histogram, cause and effect diagram, Pareto diagram, control chart, scatter diagram, flow chart, checklist) and other methods to check the quality of products or services identification and problem solving.
Quality assurance: Refers to the activities of standardizing and supervising the quality management activities of the entire organization by establishing and implementing a quality management system that meets international standards or industry standards, so as to ensure that the organization can continue to provide products that meet customer needs and market competition or service. The quality assurance of precision tool manufacturing should include the following steps:
Establish the organization’s quality policy and goals, such as following the principles of customer-oriented, continuous improvement, and full participation, to determine the quality level and direction pursued by the organization.
Establish the organization’s quality management system, such as preparing the organization’s quality manual, program documents, work instructions and other documents according to ISO 9001:2015 “Quality Management System Requirements” or IATF 16949:2016 “Automobile Industry Quality Management System Requirements” and other standards, And establish the corresponding organizational structure and distribution of responsibilities.
To implement the organization’s quality management system, such as carrying out various quality management activities in accordance with the provisions of the document, and conducting internal audits and management reviews to check and evaluate the effectiveness and applicability of the quality management system.
Improve the organization’s quality management system, such as using the PDCA (plan, execute, check, improve) cycle method to continuously improve the quality management system based on the results of internal audits and management reviews, as well as customer feedback and market changes.
Quality audit: Refers to the activities of inspecting and evaluating the quality management system of an organization or the quality of products or services through independent third-party agencies or personnel to verify whether the organization complies with relevant standards or requirements. The quality audit of precision tool manufacturing mainly includes the following categories:
System audit: refers to the audit of the organization’s quality management system, such as passing ISO 9001:2015 “Quality Management System Requirements” or IATF 16949:2016 “Automotive Industry Quality Management System Requirements” and other standards to certify the organization’s quality management system Audit to obtain the corresponding certification certificate.
Process audit: refers to the audit of a specific process or activity of the organization, such as the audit of the organization’s measurement process through ISO 10012:2003 “Measurement Management System Requirements”, to verify whether the measurement process meets the relevant requirements.
Product audit: refers to the audit of a specific product or service of the organization, such as the audit of the organization’s testing and calibration services through ISO 17025:2017 “General Requirements for the Competence of Testing and Calibration Laboratories” to verify the testing and calibration services Whether it meets the relevant requirements.
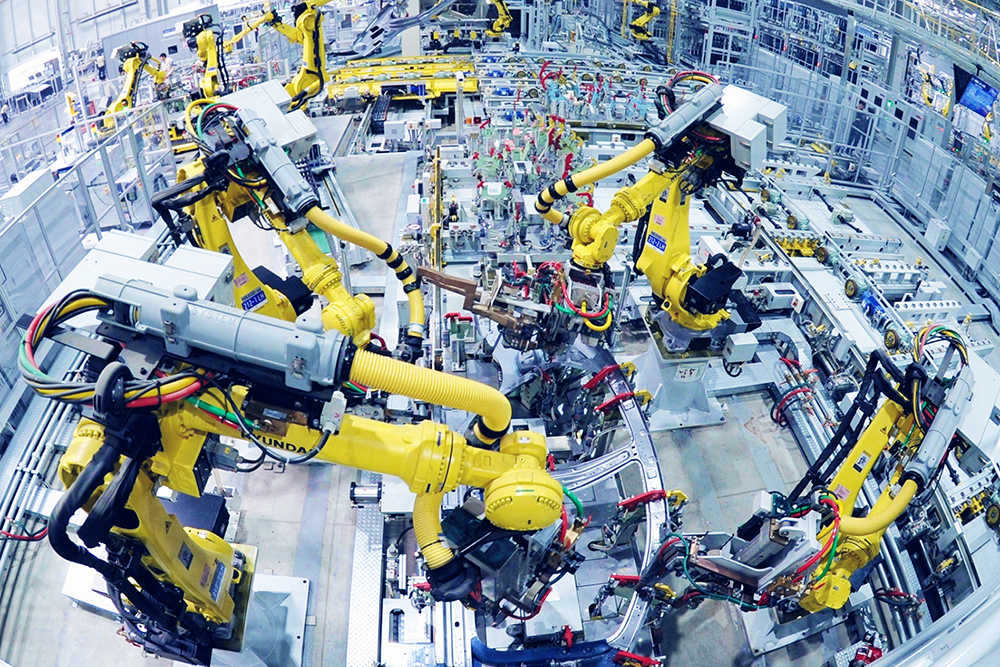
Conducive to improving production efficiency and reducing costs
In short, precision tool manufacturing is a high-tech, high-value-added, high-quality manufacturing activity that needs to follow relevant technical standards and quality management systems to ensure the quality and safety of products or services, and is also conducive to improving Productivity and cost reduction. Precision tool manufacturing enterprises should choose appropriate technical standards and quality management systems according to their own production characteristics and market demand, and constantly track and master the updates and changes of technical standards and quality management systems to adapt to market competition and customer needs.
Leave a Reply