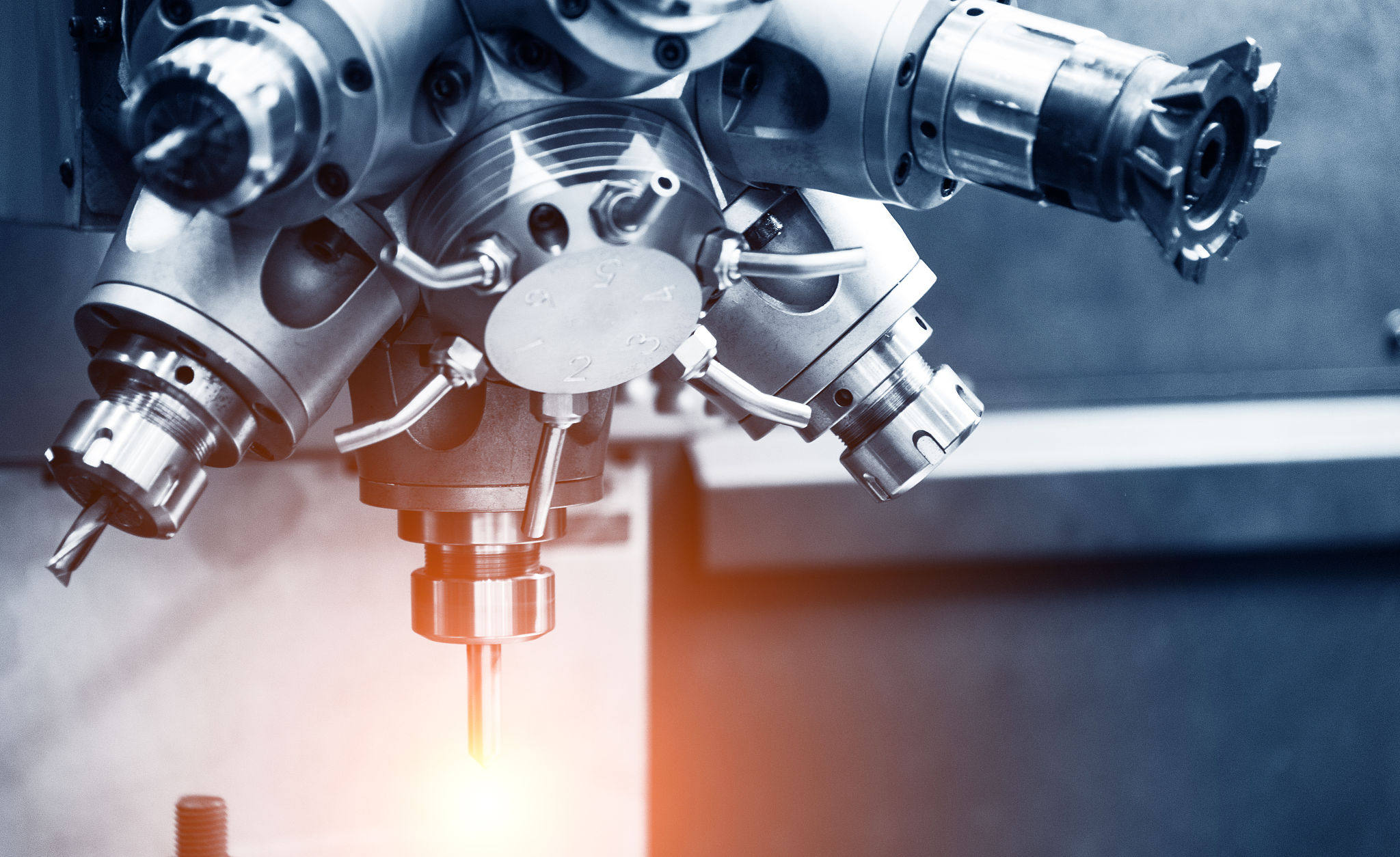
Precision Cutting Tool: How to Choose the Right One
When machining difficult-to-cut materials, such as hardened steel, titanium alloys, ceramics, and composites, superhard precision cutting tools can achieve high accuracy, efficiency, and surface quality. However, you need to consider many factors to choose the right superhard precision cutting tool for your workpiece. These factors include the tool geometry, material, coating, and machining parameters.
Here are some tips to help you select the most suitable superhard precision cutting tool.
Tool geometry: The tool geometry affects the cutting force, heat generation, chip evacuation, tool wear, and surface finish. It includes the number of flutes, the helix angle, the rake angle, the clearance angle, the cutting edge radius, and the nose shape. For example, more flutes can increase the productivity and surface quality, but reduce the chip space and increase the heat generation. A higher helix angle can reduce the cutting force and improve the chip evacuation, but increase the tool deflection and vibration. A positive rake angle can reduce the cutting force and heat generation, but weaken the tool strength.
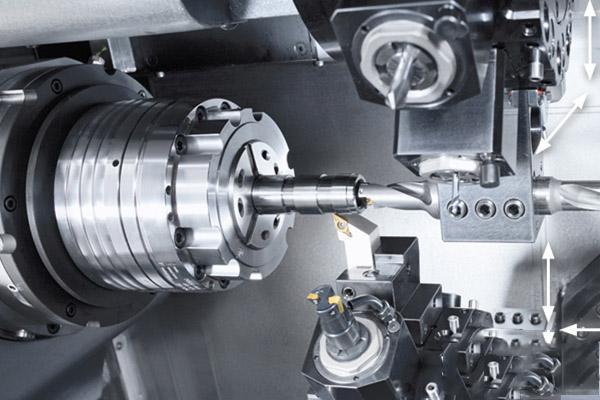
Tool material: The tool material determines the hardness, toughness, wear resistance, and thermal conductivity of the tool. The most common superhard tool materials are polycrystalline diamond (PCD) and cubic boron nitride (CBN). PCD tools have excellent wear resistance and thermal conductivity when machining non-ferrous metals, such as aluminum, copper, brass, bronze, and magnesium alloys. They can also machine some non-metallic materials, such as plastics, composites, ceramics, and wood. CBN tools have excellent wear resistance and thermal stability when machining ferrous metals, such as cast iron, hardened steel, stainless steel, nickel-based alloys, and cobalt-based alloys.
Tool coating: The tool coating can enhance the performance and extend the life of the tool by providing additional properties, such as hardness, lubricity, corrosion resistance, and oxidation resistance. The most common coatings for superhard tools are titanium nitride (TiN), titanium carbonitride (TiCN), titanium aluminum nitride (TiAlN), diamond-like carbon (DLC), and diamond coatings. For instance, TiN coating has good hardness and wear resistance when machining low-alloy steel and stainless steel. TiCN coating has better hardness and wear resistance than TiN when machining high-alloy steel and cast iron. TiAlN coating has excellent heat resistance and oxidation resistance when machining high-temperature alloys and hardened steel.
Machining parameters: The machining parameters affect the material removal rate, surface quality, tool life, and machining cost. They include the cutting speed, feed rate, depth of cut, and tool wear. For example, higher cutting speed can increase the productivity and reduce the tool wear, but also increase the cutting temperature and risk of thermal damage. Higher feed rate can increase the material removal rate, but also increase the cutting force and tool wear. Higher depth of cut can reduce the number of passes, but also increase the cutting force and temperature. Tool wear can degrade the cutting performance and surface quality, and cause dimensional errors and tool breakage. Therefore, you need to select the optimal machining parameters for superhard tools according to the specific machining conditions and requirements.
Some empirical formulas and tables can provide guidance for selecting the machining parameters for superhard tools . However, these data may not be applicable to all situations, as they depend on many factors, such as the tool geometry, material, coating, workpiece material, machine tool rigidity, cooling and lubrication conditions, etc. Therefore, it is advisable to conduct some experiments or simulations to determine the best machining parameters for superhard tools in each case. Some statistical methods, such as Taguchi method, response surface methodology, or artificial neural network, can help you optimize the machining parameters and evaluate their effects on the machining performance and quality .
In conclusion, choosing the right superhard precision cutting tool is a complex and challenging task that requires careful analysis and evaluation of various factors. By following the tips mentioned above, you can improve the machining efficiency, quality, and economy when using superhard tools.
Leave a Reply