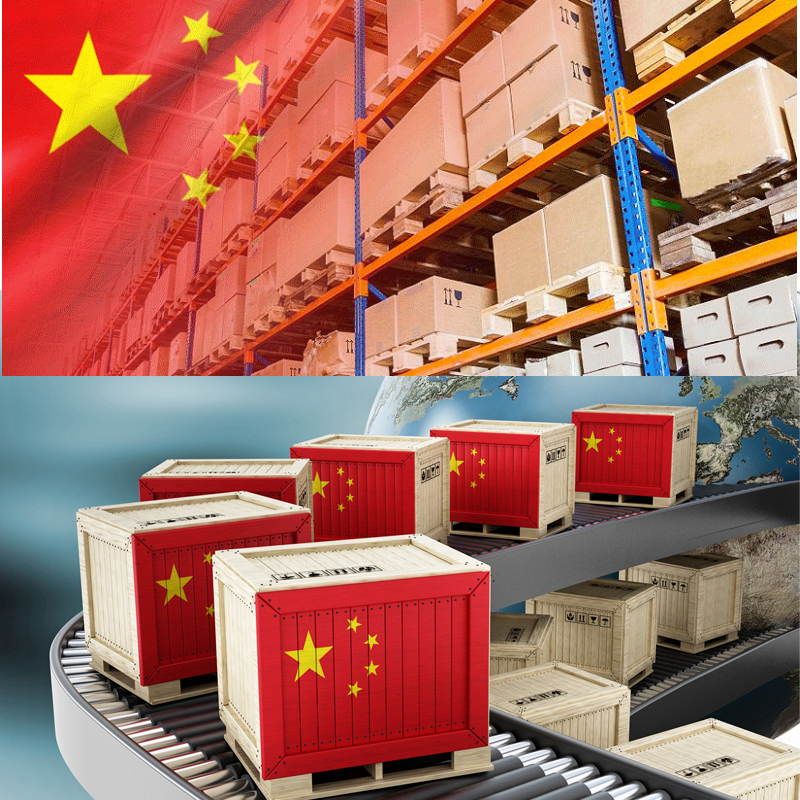
PCD/PCBN Tools: Optimization, Improvement and Innovation
PCD/PCBN (polycrystalline diamond/polycrystalline cubic boron nitride) are ultra-hard tool materials for machining difficult-to-cut materials. However, they also face some challenges, such as high cost, low toughness, and complex wear mechanisms. Therefore, they need optimization, improvement and innovation.
This article introduces some recent practices.
One practice is to optimize the tool geometry and cutting parameters for different applications. They affect the cutting performance and quality. They should match the workpiece material properties, machining requirements, and tool characteristics. For example, PCD tools performed better than PCBN tools in high speed machining of titanium alloy Ti6Al4V because they had higher wear resistance and lower chemical affinity with titanium.
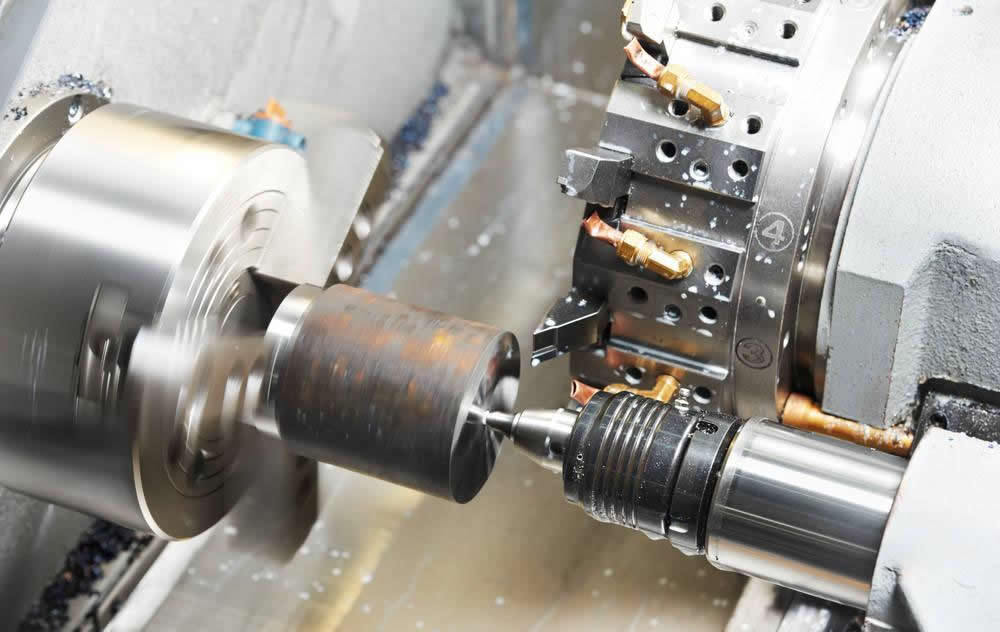
Another practice is to improve the tool material properties by modifying the composition and microstructure of PCD/PCBN. They affect the physical and mechanical properties of the tool materials. They can be modified by changing the binder phase, the diamond or cBN phase, the sintering temperature and pressure, etc. For example, PCBN tools with TiC-Co binder phase were harder and more wear-resistant than those with Al-Co binder phase in high speed turning of NiTi shape memory alloy because they had higher cBN content and lower thermal expansion coefficient.
A third practice is to innovate new tool designs or technologies that can overcome the limitations or enhance the advantages of PCD/PCBN tools. For example, PCD/PCBN composite tools combined the benefits of both materials. They had a PCD layer on one side and a PCBN layer on the other side of a cemented carbide substrate. They could machine both ferrous and non-ferrous materials by switching the cutting edges according to the workpiece material.
To sum up, optimization, improvement and innovation of PCD/PCBN tools are important for enhancing their performance and reducing their cost. Some recent practices include optimizing the tool geometry and cutting parameters; improving the tool material properties; and innovating new tool designs or technologies.
Leave a Reply