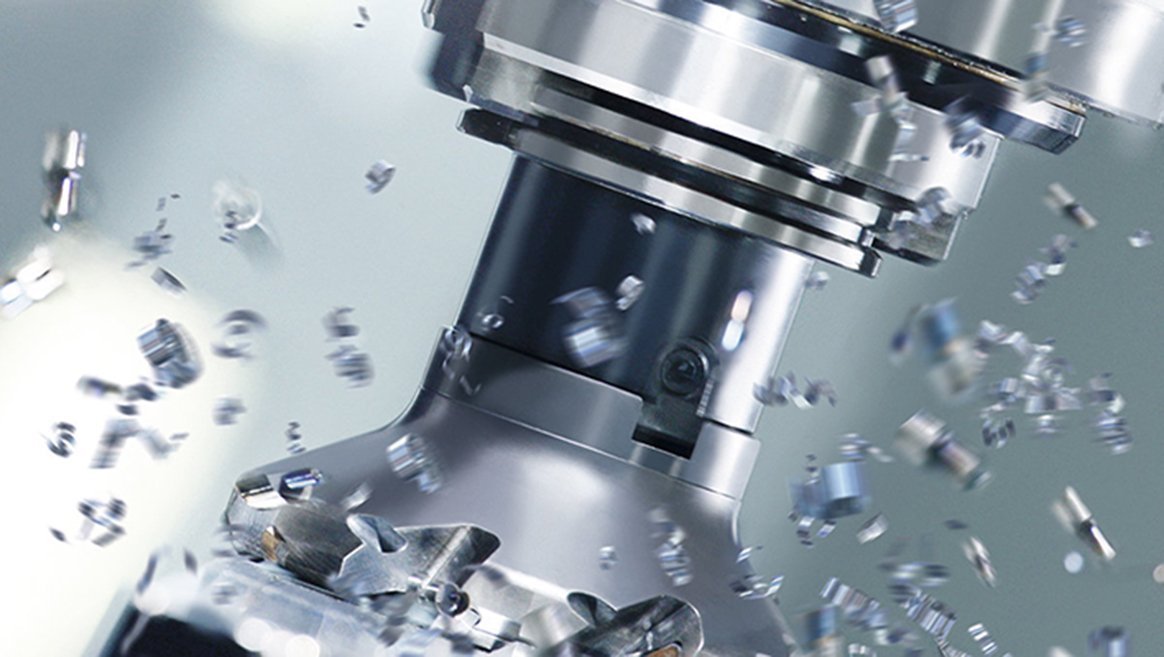
Milling Cutters: Selection of Cooling and Lubrication
Milling cutters remove material from a workpiece in machining processes. However, they often face challenges such as high cutting temperature, tool wear, surface quality, and environmental impact. Therefore, using appropriate cooling and lubrication techniques can improve the milling performance and sustainability.
There are four main categories of cooling and lubrication techniques:
dry cutting, conventional cooling, minimum quantity lubrication (MQL), and cryogenic cooling. Each technique has its own advantages and disadvantages. The best technique depends on various factors such as material properties, cutting parameters, tool geometry, and cost.
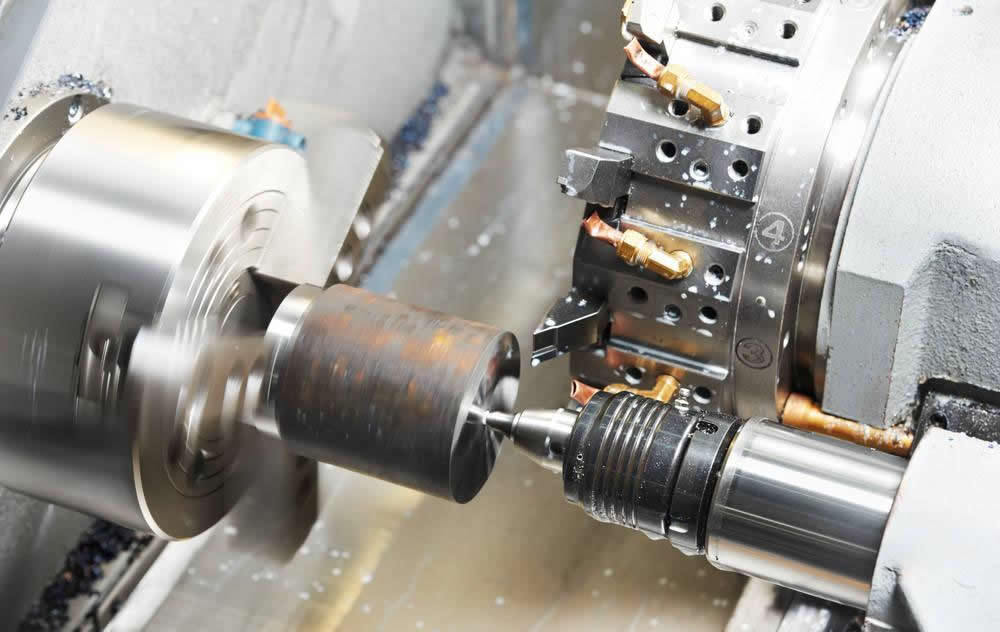
Dry cutting is the simplest and most economical technique. It does not use any coolant or lubricant during milling. Dry cutting can reduce the environmental impact and health hazards caused by cutting fluids. However, it also has some drawbacks. For example, it can cause high cutting temperature, rapid tool wear, poor surface quality, and increased cutting force.
Conventional cooling is the most common technique. It uses a large amount of water-based cutting fluid to cool and lubricate the cutting zone. Conventional cooling can effectively reduce the cutting temperature, tool wear, surface roughness, and cutting force. However, it also has some disadvantages. For instance, it can increase the cost, waste disposal, environmental pollution, health risks, and corrosion.
MQL is a technique that uses a small amount of oil-based lubricant mixed with compressed air. It forms an aerosol jet that is sprayed onto the cutting zone. MQL can provide both cooling and lubrication effects with minimal fluid consumption. MQL can reduce the cutting temperature, tool wear, surface roughness, and environmental impact compared with conventional cooling. However, it also has some limitations. For example, it may have insufficient cooling capacity, nozzle clogging, fire hazard, and compatibility issues.
Cryogenic cooling is a technique that uses extremely low-temperature gases such as liquid nitrogen or carbon dioxide to cool the cutting zone. Cryogenic cooling can provide superior cooling performance and reduce the thermal deformation of the workpiece and tool. Cryogenic cooling can also improve the surface quality and tool life compared with other techniques. However, it also has some challenges. For instance, it may require high cost, safety precautions, equipment maintenance, and thermal shock.
Leave a Reply