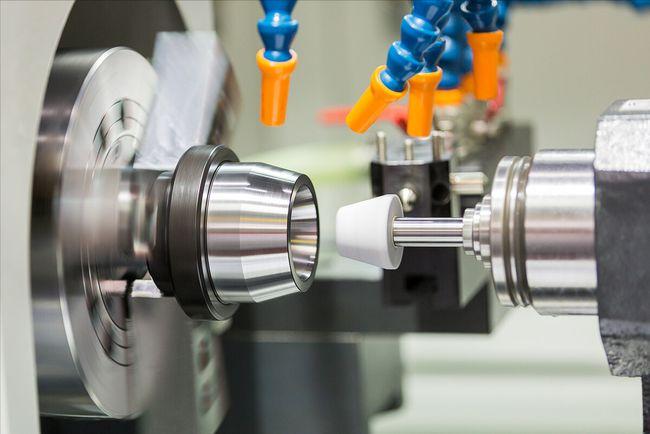
Milling Accuracy of SUS-316L Steel under Different Radius
Milling is a common machining process that uses a rotating cutting tool to remove material from a workpiece.
One of the key parameters that influences the machining performance and accuracy is the cutting edge radius (CER).
The CER is the distance from the tool tip to the intersection of the rake face and the flank face. A larger CER can reduce the stress on the cutting edge and extend the tool life.
However, it can also increase the cutting force and lower the surface quality.
Therefore, we need to optimize the CER for different milling conditions and workpiece materials.
In this post, we report on an experimental study on how CER affects cutting force, tool wear, and tool life in milling of SUS-316L steel.
SUS-316L steel is a widely used stainless steel in various industries. We used solid carbide end mills with CrTiAlN coating and different CERs from 4 to 15 μm. We prepared the CER by drag finishing (DF), which is a method that polishes the cutting edges with abrasive media. We used a dynamometer to measure the cutting force components (Fc and Ff), and a scanning electron microscope (SEM) to observe the tool wear patterns.
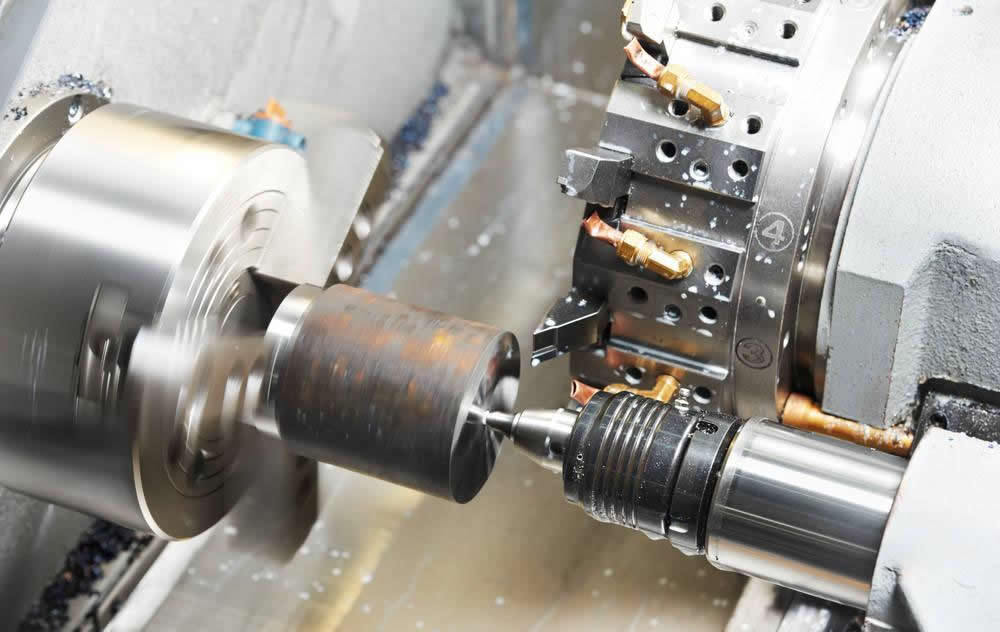
Our results showed that CER had a significant impact on the cutting performance. The cutting force Fc and feed force Ff increased by 23% and 56% at an uncut chip thickness h = 0.2 mm, respectively, when the CER increased from 4 to 15 μm. This was because of the increased ploughing effect and friction between the tool and the workpiece. The main tool wear mechanism was chipping, which resulted from the high mechanical load and thermal shock on the cutting edge. We evaluated the tool life by using a criterion of maximum flank wear width (VBmax) of 0.2 mm. The longest tool life was achieved with a nominal CER of 12 μm, which provided a balance between cutting edge strength and sharpness.
To sum up, we found that CER had a significant effect on machining accuracy in milling of SUS-316L steel. Choosing a proper CER can improve the tool performance and process reliability. However, we should also consider other factors such as cutting speed, feed rate, depth of cut, and coolant in practical applications.
Leave a Reply