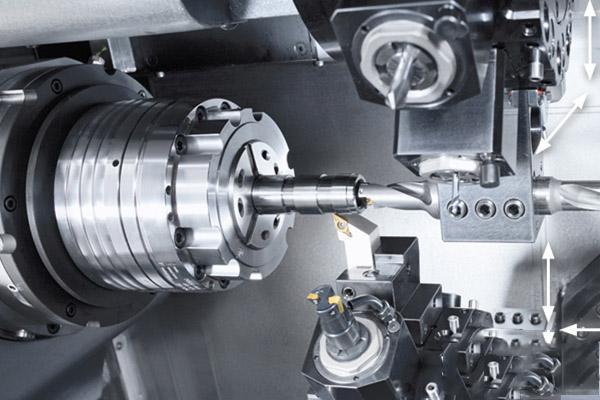
How to Choose the Right Tool Holder for Tool Fixation
Tool holders connect the cutting tool to the machine spindle. The right tool holder can improve the machining performance, quality, and efficiency.
This article discusses some factors to consider when selecting tool holders.
Type is one factor. Different types of tool holders have different pros and cons. For example, collet chucks are versatile and easy to use, but have low rigidity and high runout. End mill holders are rigid and accurate, but have low clamping force and require a Weldon flat on the tool shank. Hydraulic chucks are balanced and have high clamping force and low runout, but are expensive and require a hydraulic pump. Shrink fit holders are accurate and have low runout, but require a heating device and are difficult to change tools. Milling chucks are rigid and have high clamping force and low runout, but are heavy and expensive.
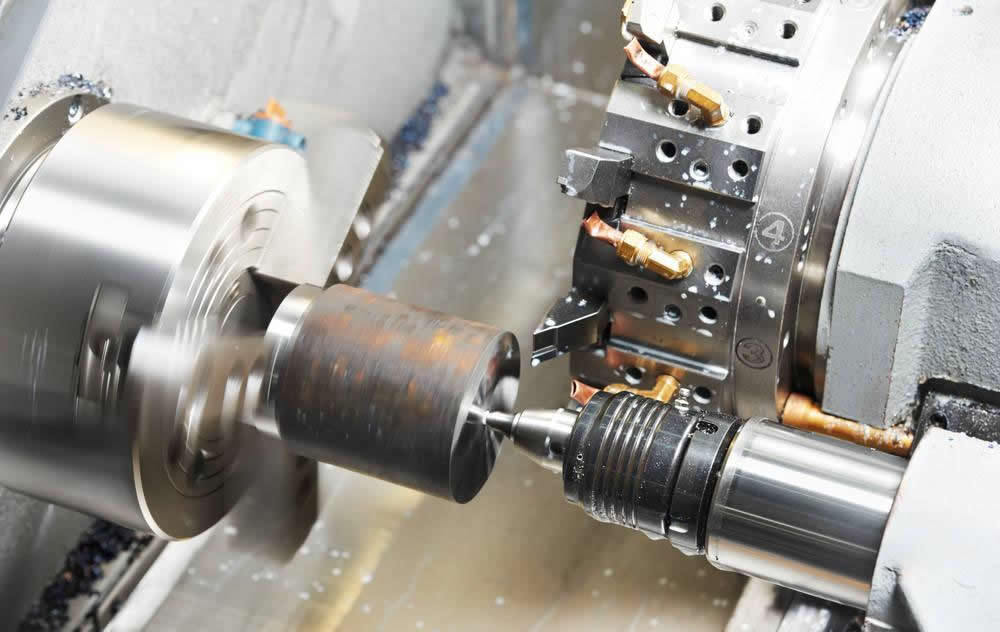
Size is another factor. The tool holder size should match the machine spindle taper and the tool shank diameter. The spindle taper is the angle of the spindle nose that determines the shape and size of the tool holder shank.
Balance is a third factor. The tool holder balance is the degree of symmetry of the tool holder mass distribution around its rotational axis. The tool holder balance affects the vibration, noise, surface finish, tool life, and spindle life of the machining process. The higher the spindle speed, the more important the tool holder balance is. The tool holder balance is measured by its grade and rotational speed.
To sum up, type, size, and balance are important factors to consider when choosing the right tool holder. The optimal choice depends on the machining application and conditions.
Leave a Reply