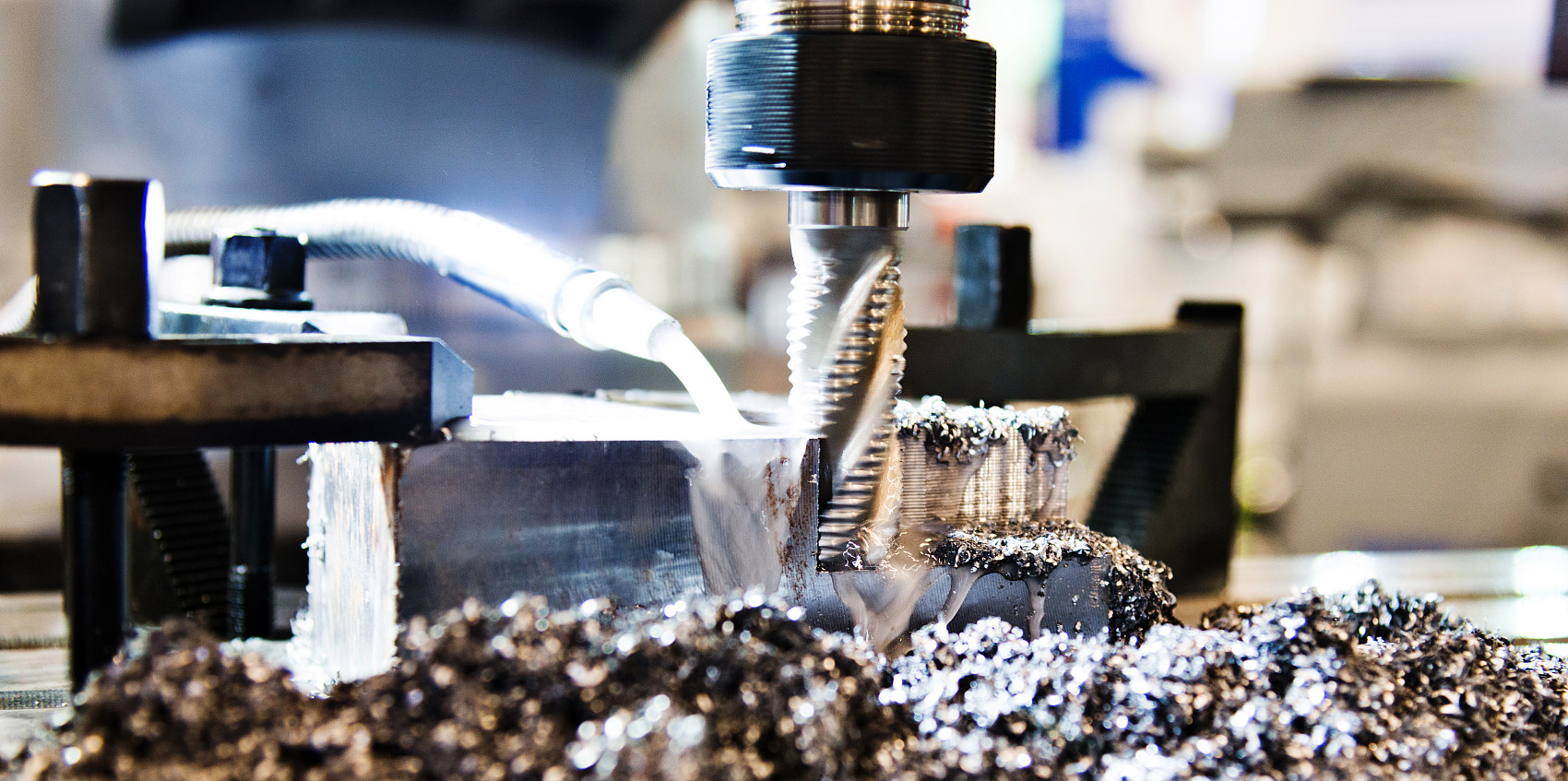
Holemaking tools: wear and life of precision tools
Holemaking is a common operation in the manufacturing of precision tools, such as drills, taps, reamers, and end mills. Hole machining tools face high cutting forces, friction, and heat, which cause tool wear and reduce tool life. Tool wear and tool life affect the quality, accuracy, and productivity of hole machining.
To optimize tool wear and tool life of hole machining tools for precision tools, you need to consider the following aspects:
– Choose a suitable tool material and coating. The tool material should have high hardness, toughness, wear resistance, and heat resistance. The tool coating should have low friction, high hardness, and good adhesion. You may choose between different types of tool materials and coatings, such as HSS, WC, PCD, or CBN.
– Select the right tool geometry and edge preparation. The tool geometry should match the hole type and size, the workpiece material and hardness, and the cutting parameters. The edge preparation involves honing or chamfering the cutting edge to improve its strength and durability.
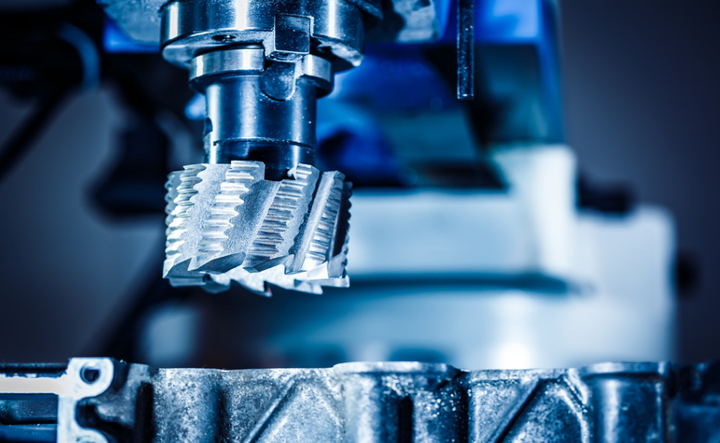
– Adjust the cutting parameters according to the tool material and geometry. The cutting parameters include cutting speed,
feed rate, depth of cut, spindle speed, etc. They affect the tool wear rate, tool life, surface quality, dimensional accuracy, and productivity of hole machining.
– Use an adequate amount and type of coolant or lubricant. Coolant or lubricant can reduce friction and heat generation, improve chip evacuation and control, prevent workpiece deformation and thermal damage, and extend tool life.
Leave a Reply