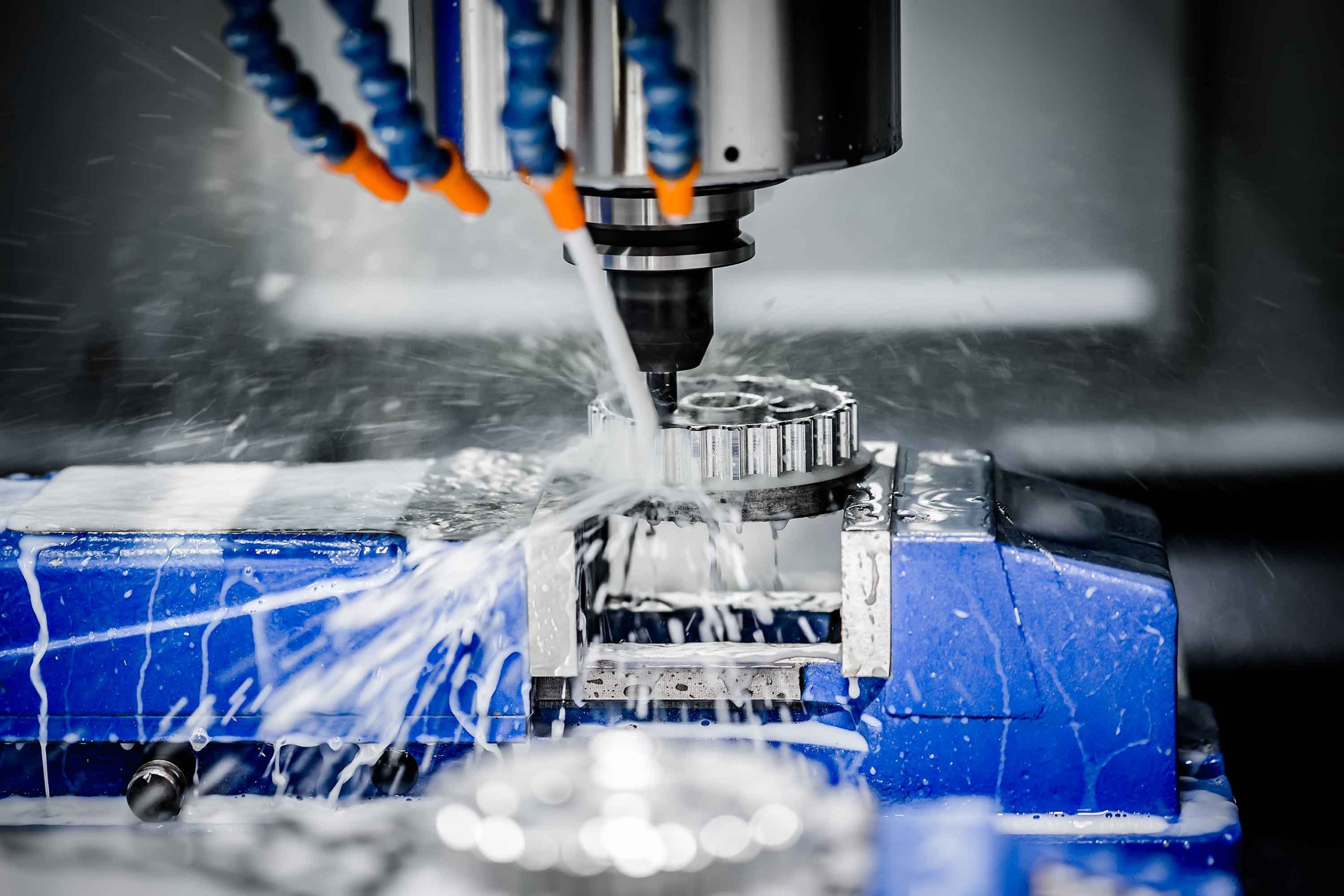
External Grooving: Application Process Tips
External grooving is a machining operation that cuts a groove on the outside of a workpiece. You can use external grooving for various purposes, such as separating a part from a bar, creating a recess for a seal or a snap ring, or reducing the weight of a component.
To achieve good results and avoid common problems in external grooving, you need to select the right cutting tools, parameters, and strategies.
Here are some tips to help you optimize your external grooving process:
– Choose a suitable insert geometry and grade. A sharp cutting edge and a positive rake angle can reduce cutting forces and heat generation in external grooving. The insert grade should also have good wear resistance and toughness to withstand the high temperatures and stresses in the groove. Depending on the material and depth of cut, you may also need a coating or a chipbreaker to improve performance and chip control.
– Select the right tool holder and clamping system. A rigid and stable tool holder can prevent vibrations and deflections that cause poor surface finish, dimensional errors, or tool breakage. The clamping system should securely hold the insert and allow easy indexing or replacement. You can choose between different types of tool holders, such as square shank, cylindrical shank, or modular systems, depending on your machine and application.
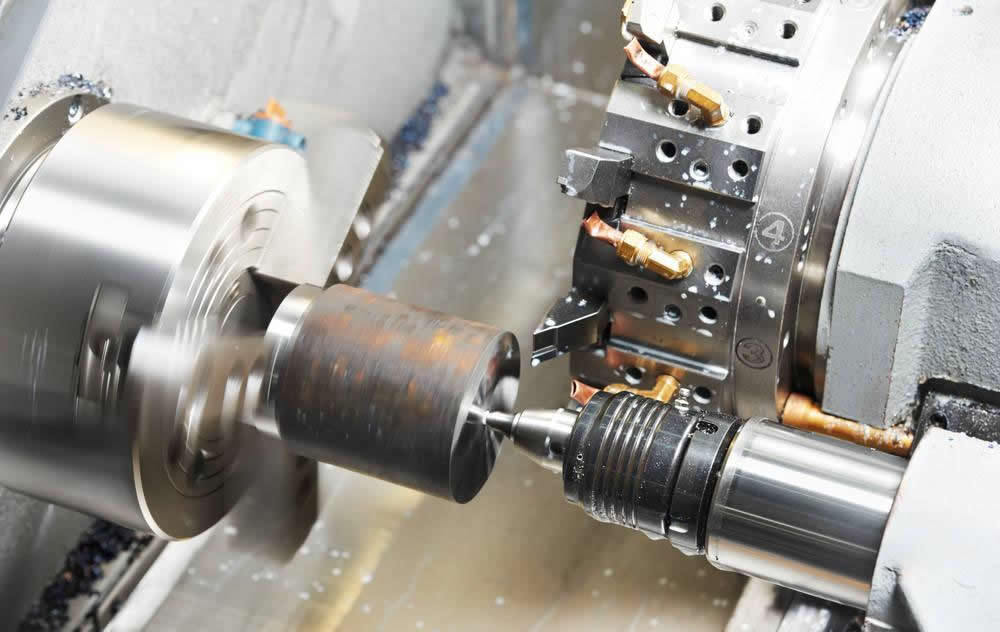
– Adjust the cutting parameters according to the groove width and depth. The cutting speed, feed rate, and depth of cut affect the tool life, surface quality, and productivity of external grooving. Generally, wider and deeper grooves require lower cutting speed and higher feed rate, while narrower and shallower grooves require the opposite. You should also consider the material properties, tool geometry, and coolant availability when setting the cutting parameters.
Leave a Reply