
Innovation and Breakthrough of Precision Tool Manufacturing in Aerospace Field
Precision tools refer to tools that can be processed, measured, and detected at the micron or nanometer level. They are widely used in aerospace, medical equipment, new energy and other fields. With the advancement of science and technology and the demand of the market, precision tool manufacturing has shown strong innovation capabilities and breakthrough achievements in the aerospace field, and has made important contributions to enhancing the international competitiveness and innovation level of my country’s aerospace industry. This article will introduce the innovation and breakthrough of precision tool manufacturing in the field of aerospace from the following aspects.
“Innovation and breakthrough of precision tool manufacturing in the field of aero-engines”
Aeroengine is the heart of the aircraft, its performance and reliability directly affect the safety and economy of the aircraft. The core components of aero-engines are turbine blades, which are subjected to extreme conditions such as high temperature, high pressure, and high-speed rotation, which place extremely high requirements on materials and processing techniques. The traditional turbine blade processing methods are mainly casting and machining, but these methods have defects, such as low casting forming precision, many internal defects, low machining efficiency, and large tool loss.
Aeroengine is the heart of the aircraft, its performance and reliability directly affect the safety and economy of the aircraft. The core components of aero-engines are turbine blades, which are subjected to extreme conditions such as high temperature, high pressure, and high-speed rotation, which place extremely high requirements on materials and processing techniques. The traditional turbine blade processing methods are mainly casting and machining, but these methods have defects, such as low casting forming precision, many internal defects, low machining efficiency, and large tool loss.
In order to solve these problems, my country’s precision tool manufacturing enterprises have realized the rapid prototyping and precision machining of turbine blades by using advanced laser additive manufacturing technology. Laser additive manufacturing technology is a technology that uses laser beams to melt and accumulate metal powder layer by layer. It has the advantages of fast forming speed, high material utilization rate, high structural complexity, and few internal defects. my country’s precision tool manufacturing enterprises have independently developed laser additive manufacturing equipment and special cutting tools suitable for turbine blade processing, and successfully realized the integrated processing process of turbine blades from the original model to finished parts. This technology not only improves the production efficiency and quality of turbine blades, but also reduces production costs and energy consumption, laying a solid foundation for my country’s independent innovation in the field of aero-engines.
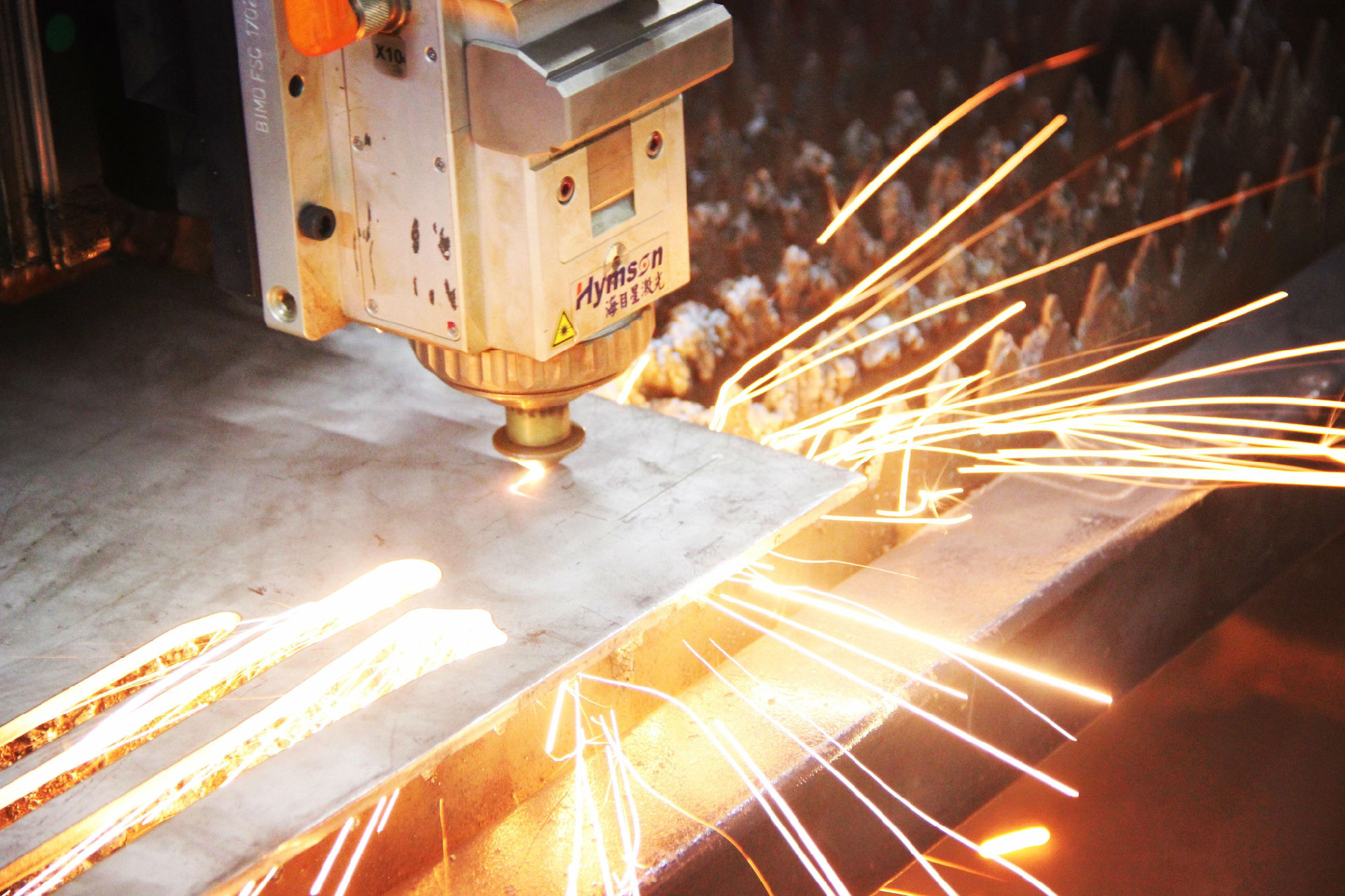
Innovation and breakthrough of precision tool manufacturing in the field of spacecraft
Spacecraft refers to man-made objects that can enter space and perform specific tasks, such as satellites, rockets, spaceships, etc. Spacecrafts face harsh conditions such as extreme temperature differences, vacuum environments, and microgravity in space, which puts extremely high requirements on their structures and functions. Traditional spacecraft manufacturing methods mainly use metal or composite materials for machining or casting, but these methods have defects, such as large structural weight, low strength, poor rigidity, low forming complexity, and long manufacturing cycle.
Spacecraft refers to man-made objects that can enter space and perform specific tasks, such as satellites, rockets, spaceships, etc. Spacecrafts face harsh conditions such as extreme temperature differences, vacuum environments, and microgravity in space, which puts extremely high requirements on their structures and functions. Traditional spacecraft manufacturing methods mainly use metal or composite materials for machining or casting, but these methods have defects, such as large structural weight, low strength, poor rigidity, low forming complexity, and long manufacturing cycle.
In order to solve these problems, my country’s precision tool manufacturing enterprises have realized the rapid prototyping and precision machining of spacecraft structural parts by using advanced ultrasonic additive manufacturing technology. Ultrasonic additive manufacturing technology is a technology that uses ultrasonic vibration to weld metal wires or metal strips layer by layer. It has the advantages of light structure weight, high strength, good rigidity, high forming complexity, and short manufacturing cycle. my country’s precision tool manufacturing enterprises have independently developed ultrasonic additive manufacturing equipment and special cutting tools suitable for the processing of spacecraft structural parts, and successfully realized the integrated processing process of spacecraft structural parts from the original model to finished parts. This technology not only improves the production efficiency and quality of spacecraft structural parts, but also reduces production costs and energy consumption, laying a solid foundation for my country’s independent innovation in the field of spacecraft.
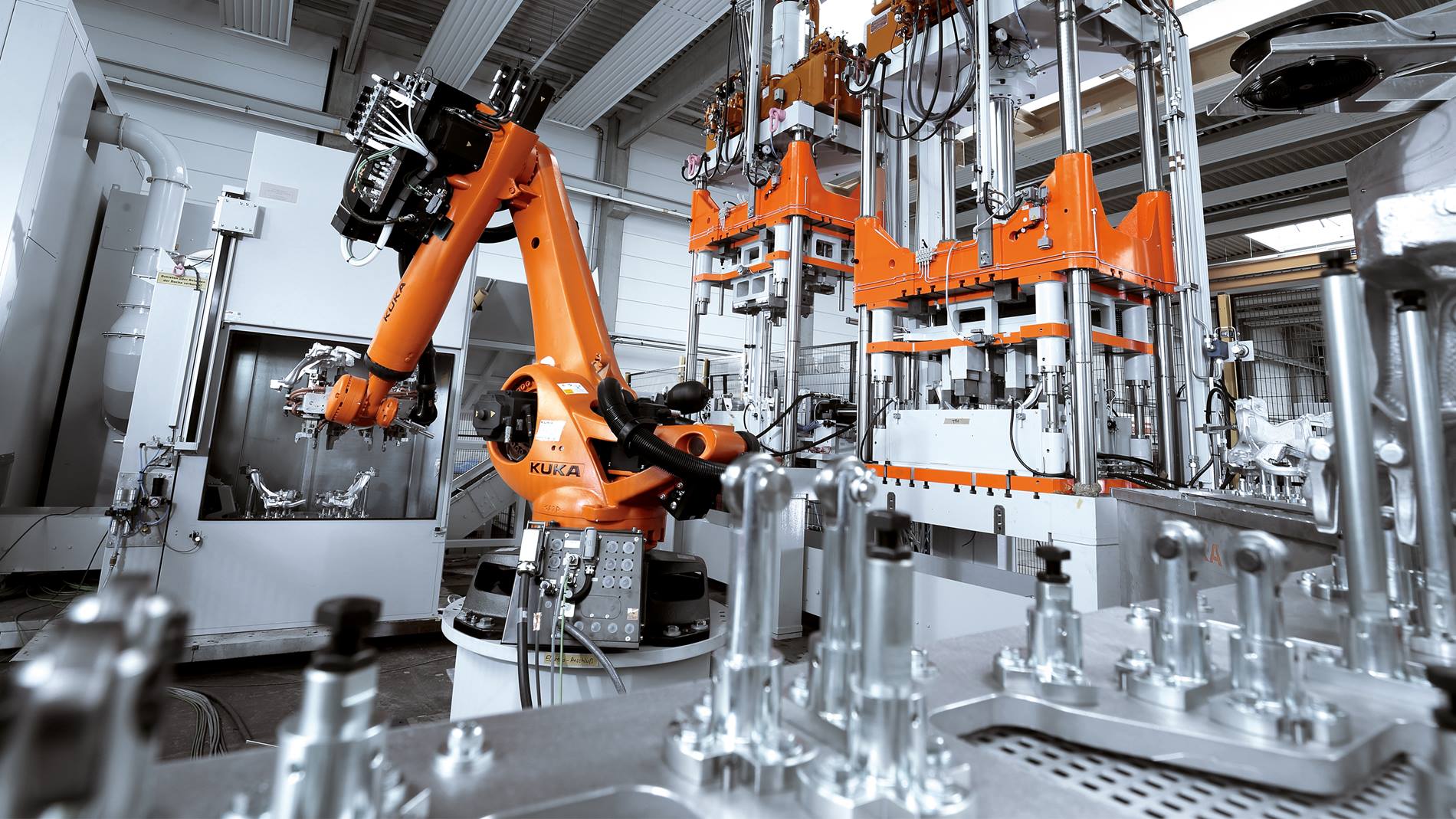
Innovation and breakthrough of precision tool manufacturing in the field of aerospace new materials
Aerospace new materials refer to new materials that can meet the special needs of the aerospace field, such as superalloys, ceramic matrix composites, carbon fiber composites, etc. Aerospace new materials play a key role in improving the performance and reliability of aerospace equipment, and are strategic resources in the aerospace field. Traditional aerospace new material preparation methods mainly use powder metallurgy, chemical vapor deposition, physical vapor deposition and other methods, but these methods have defects, such as large raw material consumption, large environmental pollution, uneven composition, and many defects.
In order to solve these problems, my country’s precision tool manufacturing enterprises have realized the rapid preparation and precision processing of new aerospace materials by using advanced electron beam cooling bed technology. Electron beam cooling bed technology is a technology that uses electron beams to melt and solidify metal powder layer by layer. It has the advantages of high raw material utilization rate, low environmental pollution, uniform composition, and few defects. my country’s precision tool manufacturing enterprises have independently developed electron beam cooling bed equipment and special cutting tools suitable for the preparation of new aerospace materials, and successfully realized the rapid preparation and precision processing of various aerospace new materials such as superalloys and ceramic matrix composite materials. This technology not only improves the production efficiency and quality of new aerospace materials, but also reduces production costs and energy consumption, laying a solid foundation for my country’s independent innovation in the field of new aerospace materials.
Aerospace new materials refer to new materials that can meet the special needs of the aerospace field, such as superalloys, ceramic matrix composites, carbon fiber composites, etc. Aerospace new materials play a key role in improving the performance and reliability of aerospace equipment, and are strategic resources in the aerospace field. Traditional aerospace new material preparation methods mainly use powder metallurgy, chemical vapor deposition, physical vapor deposition and other methods, but these methods have defects, such as large raw material consumption, large environmental pollution, uneven composition, and many defects.
In order to solve these problems, my country’s precision tool manufacturing enterprises have realized the rapid preparation and precision processing of new aerospace materials by using advanced electron beam cooling bed technology. Electron beam cooling bed technology is a technology that uses electron beams to melt and solidify metal powder layer by layer. It has the advantages of high raw material utilization rate, low environmental pollution, uniform composition, and few defects. my country’s precision tool manufacturing enterprises have independently developed electron beam cooling bed equipment and special cutting tools suitable for the preparation of new aerospace materials, and successfully realized the rapid preparation and precision processing of various aerospace new materials such as superalloys and ceramic matrix composite materials. This technology not only improves the production efficiency and quality of new aerospace materials, but also reduces production costs and energy consumption, laying a solid foundation for my country’s independent innovation in the field of new aerospace materials.
In short, precision tool manufacturing has demonstrated strong innovation capabilities and breakthrough achievements in the aerospace field, and has made important contributions to enhancing the international competitiveness and innovation level of my country’s aerospace industry. Precision tool manufacturing enterprises should seize opportunities, overcome challenges, continuously improve technical level and product quality, and contribute more to the development of my country’s aerospace field.
Leave a Reply