
Technological innovation and development trend of precision tool manufacturing
Precision tool manufacturing refers to the technology and process of precision machining and testing of various materials using high-precision machine tools, cutting tools, measuring instruments and other equipment. Precision tool manufacturing is widely used in high-tech fields such as aerospace, automobiles, molds, electronic information, and medical equipment, and is an important support and guide for modern manufacturing.
With the progress of science and technology and the demand of the market, precision tool manufacturing is facing new development opportunities and challenges. In order to improve the level and competitiveness of precision tool manufacturing, it is necessary to continuously carry out technological innovation and optimization, master new technical methods and technological means, and meet the requirements of higher machining accuracy and surface quality. This article will introduce the technological innovation and development trend of precision tool manufacturing from the following aspects:
“Precision Forming Technology”
Precision forming technology refers to the technology of obtaining the desired shape and size by applying external force to the material to produce plastic deformation. Precision forming technology includes precision casting, precision forging, precision molding, plastic processing, thin plate precision forming, etc.
1. Precision forming technology has the following advantages:
(1) Save materials and energy, reduce processing procedures and equipment, and reduce production costs;
(2) Improve production efficiency and product quality, and enhance product performance and reliability;
(3) It is suitable for the processing of various materials and complex structural parts, expanding the types and scope of products.
The development trend of precision forming technology is mainly reflected in the following aspects:
(1) Precision. With the complication and miniaturization of product functions, the requirements for forming precision and surface quality are constantly increasing, from millimeter level to micron level or even nanometer level. For example, there are currently technologies that use unconventional energy sources such as ultrasonic vibration cutting, electric discharge machining, and laser processing to process micro-holes, which can realize micro-deep holes with a diameter of less than 50 μm.
(2) Intelligence. Intelligence refers to the use of information technology, artificial intelligence, Internet of Things and other means to realize real-time monitoring, analysis, control and optimization of the forming process, improve forming efficiency and quality, and reduce costs and resource consumption. For example, use sensors, cloud computing, machine learning and other technologies to realize intelligent diagnosis and predictive maintenance of machine tool status, tool wear, forming parameters, etc.; use digital twin technology to realize modeling and simulation of the physical world and optimize forming solutions and process.
(3) Diversification. Diversification refers to the use of various forming methods and combinations according to different material properties, product shapes, forming requirements, etc., to achieve efficient and high-quality forming of complex structural parts, functional parts, special-shaped parts, etc. For example, using precision forging technologies at different temperatures such as hot precision forging, cold precision forging, warm precision forging, composite precision forging, and isothermal precision forging, suitable forming can be carried out according to different materials and workpieces; Different methods of precision molding technology, such as the principle of precision forming and isobaric forming process, can realize high-precision forming of metal and non-metal materials.
2. Precision cutting technology
Precision cutting technology refers to the technology of using tools to remove chips from materials to obtain the desired shape and size. Precision cutting technology includes precision grinding, precision cutting, honing, grinding, polishing and so on.
Precision cutting technology has the following advantages:
(1) It is suitable for processing various materials and hardness, and can achieve high surface quality and low surface stress;
(2) It can realize high-speed and efficient processing, improve productivity and save energy;
(3) It can realize high-precision and high-smooth processing, and meet the processing requirements of micron or even nanometer.
The development trend of precision cutting technology is mainly reflected in the following aspects:
(1) High speed. High speed refers to increasing cutting speed and feed rate to improve processing efficiency and quality. High-speed cutting can reduce the friction and thermal influence of chips on the tool and workpiece surface, reduce tool wear and workpiece deformation, and improve surface quality and dimensional stability. At present, there is a technology for high-speed cutting using superhard tools, which can achieve a spindle speed of tens of thousands of revolutions per minute and a feed rate of several kilometers per minute.
(2) Precision. Precision refers to improving machining accuracy and surface quality to meet higher machining requirements. With the complexity and miniaturization of product functions, the requirements for processing accuracy and surface quality are constantly increasing, from micron level to submicron level or even nanometer level. At present, there are ultra-precision cutting technologies using ultra-precision machine tools and single crystal diamond tools, which can achieve dimensional accuracy higher than 0.1 μm and surface roughness less than 0.025 μm.
(3) Intelligence. Intelligence refers to the use of information technology, artificial intelligence, Internet of Things and other means to realize real-time monitoring, analysis, control and optimization of the cutting process, improve cutting efficiency and quality, and reduce costs and resource consumption. For example, use sensors, cloud computing, machine learning and other technologies to realize intelligent diagnosis and predictive maintenance of machine tool status, tool wear, cutting parameters, etc.; use digital twin technology to realize modeling and simulation of cutting process and optimize cutting plan and process.
3. Precision detection technology
Precision detection technology refers to the technology of measuring and evaluating the size, shape, position and surface state of workpieces by using various instruments and equipment. Precision detection technology is an important part of precision tool manufacturing and a key link to ensure product quality and performance.
Precision detection technology has the following advantages:
(1) It can conduct comprehensive, accurate and rapid detection of workpieces, and improve the product qualification rate and one-time pass rate;
(2) The workpiece can be detected online, offline or remotely to improve the detection efficiency and flexibility;
(3) The detection data can be stored, analyzed, fed back and managed to improve the detection level and intelligence.
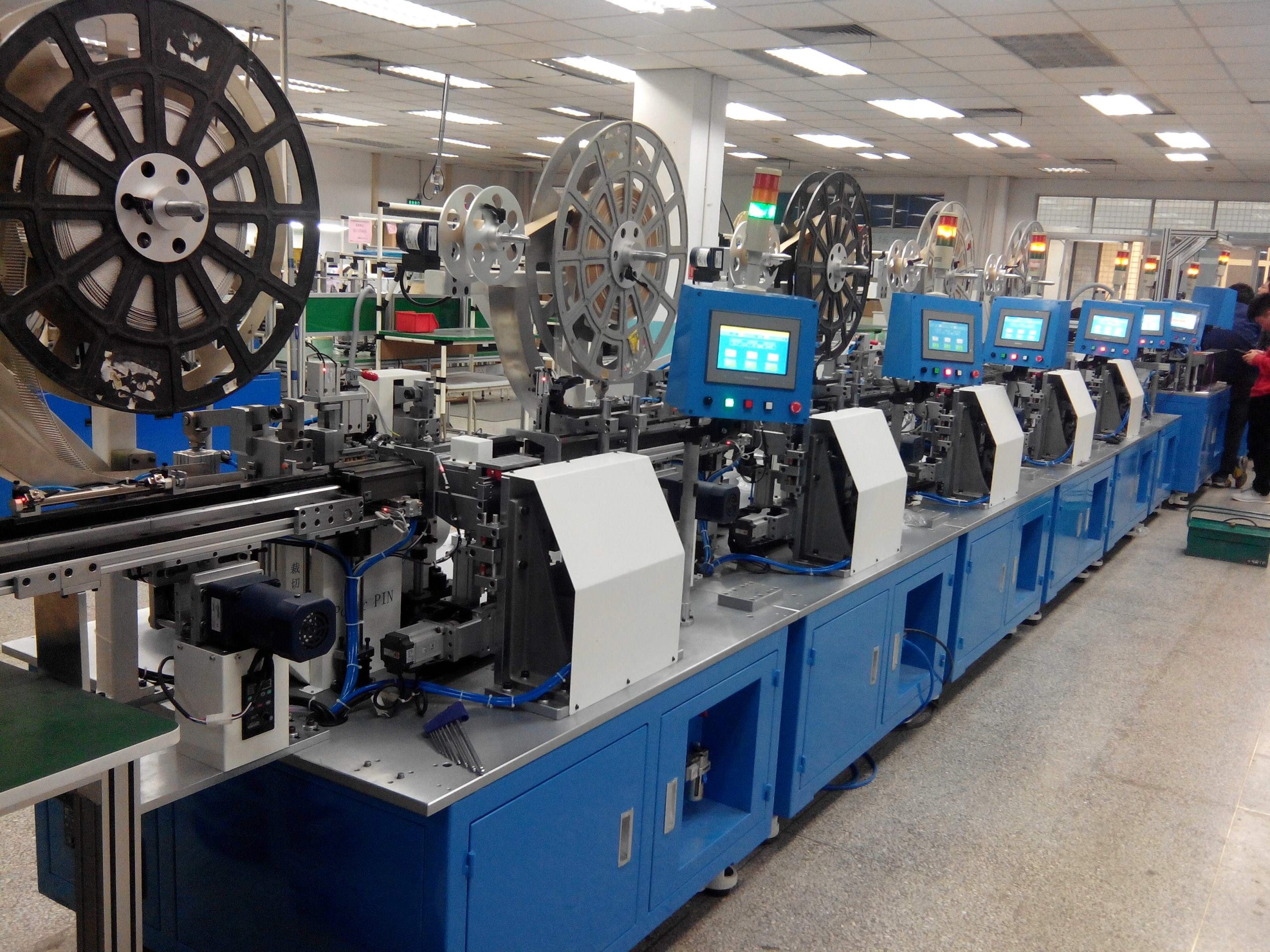
The development trend of precision detection technology
The development trend of precision detection technology is mainly reflected in the following aspects:
(1) High speed. High-speed refers to the improvement of detection speed and frequency to meet the requirements of high-speed and efficient production. High-speed inspection can reduce inspection time and cost, improve production efficiency and quality. At present, there are technologies using non-contact detection methods such as lasers, ultrasonic waves, and electromagnetic waves, which can realize rapid scanning and dynamic monitoring of workpieces.
(2) Precision. Precision refers to improving detection accuracy and resolution to meet higher detection requirements. With the complexity and miniaturization of product functions, the requirements for detection accuracy and resolution continue to increase, from micron to submicron or even nanometer. At present, there are technologies using nano-scale detection methods such as nano-probes and atomic force microscopes, which can realize nano-scale detection of the surface morphology and structure of workpieces.
The development trend of precision detection technology is mainly reflected in the following aspects:
(1) High speed. High-speed refers to the improvement of detection speed and frequency to meet the requirements of high-speed and efficient production. High-speed inspection can reduce inspection time and cost, improve production efficiency and quality. At present, there are technologies using non-contact detection methods such as lasers, ultrasonic waves, and electromagnetic waves, which can realize rapid scanning and dynamic monitoring of workpieces.
(2) Precision. Precision refers to improving detection accuracy and resolution to meet higher detection requirements. With the complexity and miniaturization of product functions, the requirements for detection accuracy and resolution continue to increase, from micron to submicron or even nanometer. At present, there are technologies using nano-scale detection methods such as nano-probes and atomic force microscopes, which can realize nano-scale detection of the surface morphology and structure of workpieces.
(3) Intelligence. Intelligence refers to the use of information technology, artificial intelligence, Internet of Things and other means to realize real-time monitoring, analysis, control and optimization of the detection process, improve detection efficiency and quality, and reduce costs and resource consumption. For example, use sensors, cloud computing, machine learning and other technologies to realize intelligent processing and decision support for detection data; use digital twin technology to realize modeling and simulation of the detection process, and optimize detection schemes and processes.
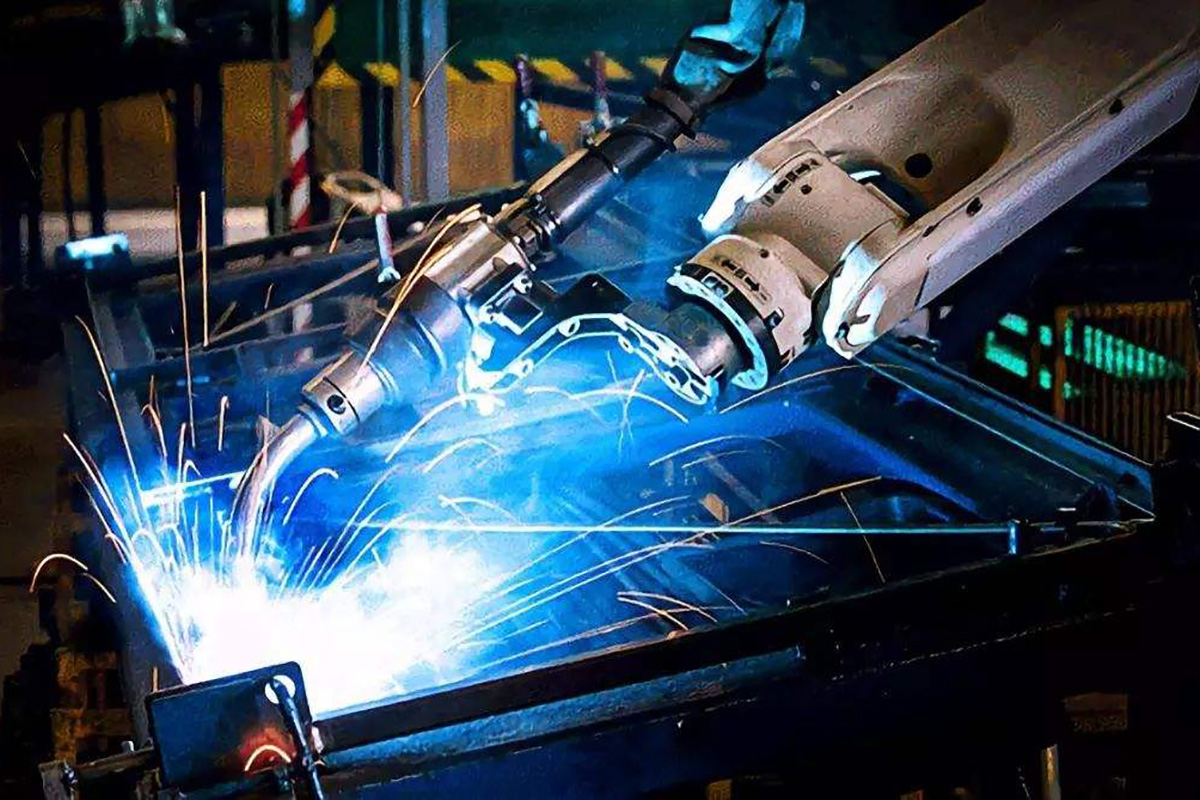
In short, precision tool manufacturing is an important part of modern manufacturing and an important direction for future manufacturing development. In order to improve the level and competitiveness of precision tool manufacturing, it is necessary to continuously carry out technological innovation and optimization, master new technical methods and technological means, and meet the requirements of higher machining accuracy and surface quality. This paper introduces the technological innovation and development trend of precision tool manufacturing from three aspects: precision forming technology, precision cutting technology and precision testing technology, hoping to inspire and help readers.
Leave a Reply